Vehicle Service Facility Requirements & Support
Environmental Services
The City of Petaluma Environmental Services team is dedicated to pollution prevention, stormwater management, and protecting City infrastructure. We offer resources and information to help maintain the health and wellness of our community by preventing pollution in our sewer and storm collections systems. If you have a stormwater concern, please call the Environmental Services line at (707) 776-3777 or email [email protected].
Pollution Prevention for Vehicle Services Facilities
Vehicle services facilities such as auto repair shops, autobody facilities, fleet maintenance centers, car washing facilities, and gas filling stations generate wastewater that may contain oil, grease, heavy metals, detergents, and other pollutants harmful to the environment, the sewer collection system, and the Wastewater Treatment Plant (WWTP). These pollutants can also create dangerous situations in sewer and stormwater collections systems. Oils can solidify in sanitary sewer lines causing blockages which lead to sanitary sewer overflows causing public health issues. Hydrocarbons can create explosive conditions in sewer lines and pump stations that are dangerous to City staff and the general public. WWTP’s are not equipped to treat hazardous waste. These types of waste can disrupt the biological treatment processes at the WWTP, allowing hazardous substances to pass through treatment and into the environment.
The facilities listed above may be required to install, operate, and maintain an oil-water separating device and/or catch basins in compliance with the plumbing code to address the potential hazards associated with these discharges.
Vehicle Services Facilities FAQs
- What is an oil-water separator?
- Is my facility required to have an oil-water separator?
- How does an oil-water separator work?
- How do I have my oil-water separator cleaned, and how often must I clean the device?
- What is inspected?
- What are the Best Management Practices?
- How is compliance determined?
- What if the inspector determines the auto service facility is not in compliance?
What is an oil-water separator?
An oil-water separator removes oil, grease, and hydrocarbons from wastewater before they can be discharged into the sanitary sewer or accidentally released into the stormwater system. Oil-water separators prevent oil, grit, sludge, and other pollution from entering municipal WWTPs and natural waterways.
Is my facility required to have an oil-water separator?
Per Petaluma Municipal Code 14.48.110: “All new gasoline filling stations, garages, self-service automobile washers, autobody facilities, and other public wash racks where vehicles are washed shall install catch basins in conformity with the plumbing code in accordance with a permit obtained from the building official. In the event any existing premises do not have a catch basin and the sewer line servicing the facility stops up due to grit or slime in the sewer lines, then the owner or operator of such premises shall be required to modify these facilities to construct a catch basin as a condition of continuing use of the system. No stormwater shall be diverted to these catch basins. No wash rack waste shall be diverted into the stormwater system…”
How does an oil-water separator work?
Oil-water separators operate separate substances by their differing density properties inside the device.
- Oil, being lighter than water, floats to the surface of the device.
- Solids, being heavier than water, settle at the bottom of the device.
- The treated, cleaner wastewater accumulates in the middle of the device after the separation of oils and solids. The middle of the device is where the effluent pipe is located, allowing for the treated water to exit the device for further treatment or discharge.
Oil-water separators require periodic maintenance to remove accumulated oils and solids and maintain proper functionality of the device.
How do I have my oil-water separator cleaned, and how often must I clean the device?
Typically, the devices are pumped out by a licensed waste pumping and hauling service. The removed contents are required to be adequately and appropriately disposed of at a permitted disposal facility based on the contents of the separator. The contents may qualify as hazardous waste and must be serviced by a certified hazardous waste hauler. Records of service and maintenance of the device must be maintained on site and available upon inspection for the previous three (3) years.
The frequency in which the device needs to be cleaned is largely dependent on the business activities and operations at the facility. Facilities with higher amounts of oils and solids entering the system require more frequent cleaning than facilities with less accumulation. Larger devices may require less cleaning frequency than smaller devices as there is more room for accumulation of oils and solids. Periodic monitoring of the accumulation in the device can help determine a proper cleaning frequency for your specific device.
Smaller devices, such as catch basins, may be self-cleaned. The contents removed from these devices must be appropriately containerized and disposed of in accordance with waste haulers requirements.
A common frequency for cleaning and servicing a large oil-water separator is on an annual basis, but the necessary frequency depends on the specifics of the facility’s operation. Routine checks of the loading levels of the separator can help establish a proper cleaning frequency. The City offers courtesy checks on oil/water separator devices to help determine a cleaning frequency that should keep the device in compliance with proper maintenance. Email [email protected], or call 707-776-3777 to schedule a courtesy inspection with City staff.
Inspections
The City conducts inspections of vehicle service facilities with and without oil-water separators to ensure compliance with wastewater discharges and ensure proper stormwater protections and waste disposal practices.
Inspections are scheduled in advance with the owner, manager, or whoever manages the oil water separator system and/or the facility.
The City aims to inspect auto service facilities every three (3) years.
Depending on the size of the facility, inspections typically take 30 to 45 minutes.
What is inspected?
The oil-water separator.
- The City will inspect to ensure the device is properly plumbed to service all the possible discharge locations of process wastewater generated from the facility.
- The components of the separators will also be observed and inspected for proper functionality. This includes influent and effluent plumbing piping, baffle walls, standpipes, overall condition, and anything else related to the proper function of the separator.
- The loading levels of oils and solids accumulation will be measured in the oil-water separator to determine if the device is functioning properly and is not overloaded. An oil-water separator with more than 25% accumulation of both oils at the surface, and solids at the bottom, may be considered overloaded and out of compliance resulting in a failed inspection.
Stormwater and Sewer Drain Management.
- The City will inspect floor drains, loading dock areas, sanitary sewer lines, stormwater inlets, chemical and waste storage accumulation areas, and any other location of possible discharge to the sanitary sewer or Municipal Separate Storm Sewer System (MS4) for evidence of chemical or oil stains that may indicate an occurrence of an illicit discharge or improper disposal of waste.
- Secondary containment will be inspected for spill protection and prevention of discharges to the sewer or MS4.
- Spill kits will be inspected for their presence and location in relation to potential accidental chemical releases.
- Wash water and mop water disposal practices and discharge locations will be reviewed and identified.
- Any steam cleaning or pressure washing activities will be reviewed for adequate waste management.
- The dumpster and trash receptacles will be inspected ensuring that they are covered and not leaking.
Record Keeping.
- The City will inspect the most recent pumping and service records for the oil-water separator.
- Three (3) years of records and maintenance from servicing the device are required to be maintained onsite and available upon inspection.
- Hazardous waste disposal manifests will be reviewed and assessed for accuracy and evaluated to ensure all hazardous waste generated onsite is properly accounted for and disposed of appropriately.
- The spill response plan for the facility will be reviewed or requested as necessary.
- Employee training records for pollution prevention and hazardous waste management and disposal are required to be maintained onsite and available upon inspection.
What are the Best Management Practices?
- Use dry cleanup methods such as sweeping and using rags and absorbents to clean spills and dirty areas before washing with water.
- Use biodegradable and/or less toxic products and detergents to avoid harsh chemicals that can contribute to pollution of waterways and the environment.
- Neutralize discharges to permitted pH levels between 5 to 10.5 SU prior to discharge.
- Recycle wash water using closed-loops systems to reduce water consumption and pollution.
- Limit vehicle washing on pavement by washing over permeable surfaces or in designated wash bays with collection systems.
- Prevent spills by properly storing and labeling chemicals and keeping containers sealed and labeled.
- Provide staff training on chemical handling and spill response to ensure staff knows how to contain, clean up, and dispose of hazardous materials safely and appropriately.
- Ensure adequate secondary containment in chemical storage areas.
- Place drip pans under vehicles that are being worked on or are leaking.
- Always have shop rags on hand for small spills.
- Use a funnel when pouring liquids like lubricants or motor oil and place a tray underneath to catch spills.
- Do not store chemicals or wastes in areas that can drain to the sewer or storm drains in the event of an accidental release.
Stormwater Pollution Prevention
- Use secondary containment and spill-proof containers with berms or trays to avoid illicit discharges to the City’s stormwater infrastructure.
- Cover work areas and perform maintenance and fueling under covered areas to prevent rainwater contamination.
- Maintain spill kits with absorbent materials, booms, and drain covers for quick spill response.
- Regularly inspect storm drains for indications of contamination, and clean inlets when necessary.
- Help filter contaminates before they reach stormwater systems by using permeable pavement.
How is compliance determined?
- The oil-water separator is plumbed correctly and is not exceeding the loading limitations of the device. An oil water separator with over 25% accumulation of oils and solids may be considered overloaded and out of compliance.
- Service maintenance and waste disposal records are available at the time of inspection for cleaning and removal of the contents of the device.
- Hazardous waste disposal records and manifests are on site and available during inspection.
- Records for the past three (3) years are maintained onsite.
- No evidence of illicit discharges to the sanitary sewer system or MS4 are identified at time of inspection.
What if the inspector determines the auto service facility is not in compliance?
If the facility is found to be out of compliance upon inspection it may receive a:
- Warning – A warning identifies areas of deficiency encountered during the inspection that need to be fixed or corrected. The City will provide a corrective action(s) that will be required to be implemented by a certain date or prior to the next inspection.
- Notice of Violation – A notice of violation identifies circumstance(s) that are in violation of the City’s Sewer Use Ordinance or Stormwater Management and Pollution Control Ordinance. The notice will identify the specific violation or violations encountered during inspection and the requirements the facility must follow to remediate or correct the violation. Continued notices of violation may result in an escalation of enforcement by the City which may result in monetary fines or disconnections of utility services at the discretion of the City of Petaluma.
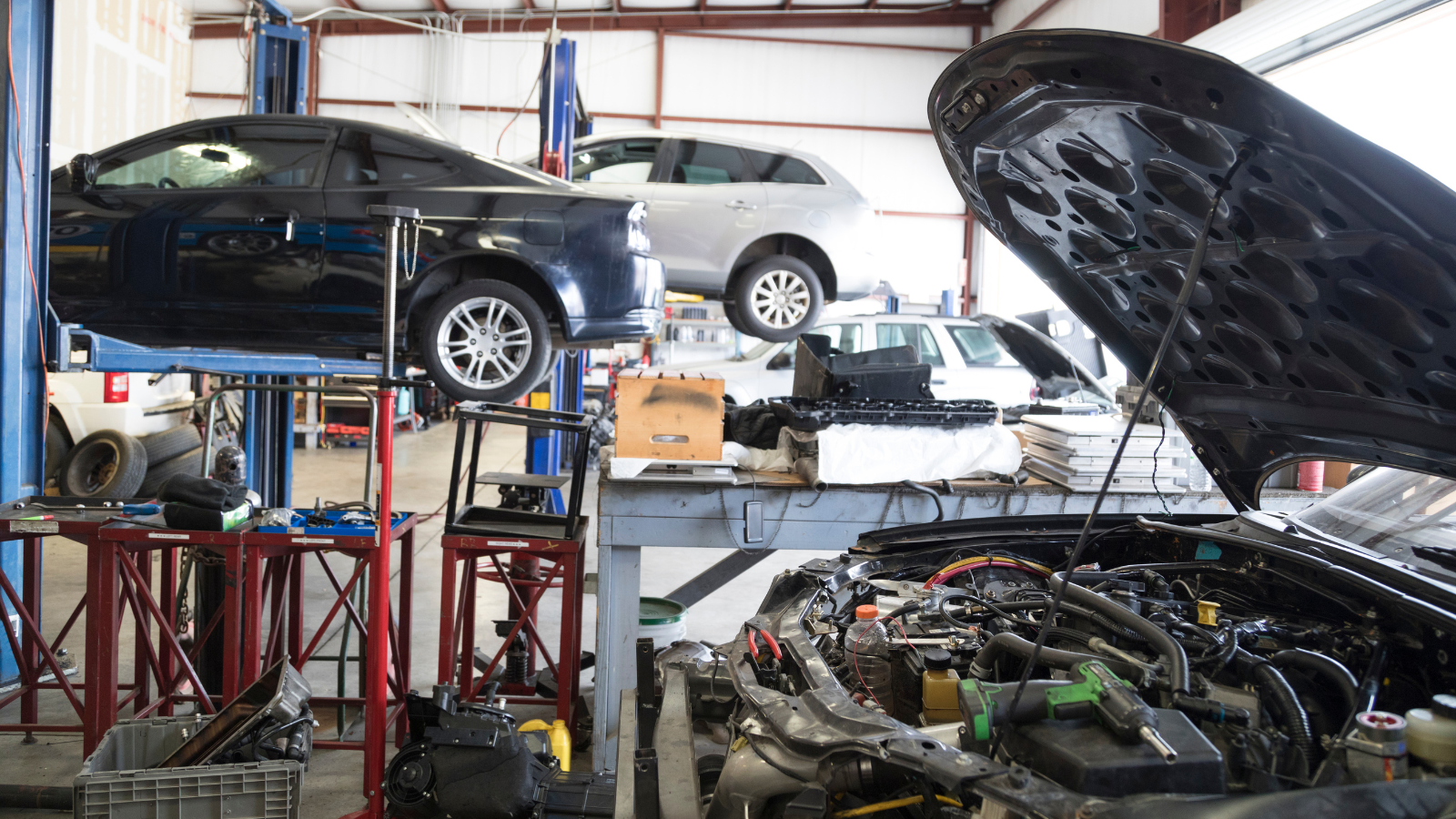